防腐层与阴极保护联合防护体系是长输管线广泛采用的土壤腐蚀控制措施。三层聚乙烯 (3PE) 防腐在国内外重要长输管线工程中大量使用。3PE涂层体系长期服役过程中,在涂层/金属界面应力、阴极保护、土壤微生物、植物根系等因素作用下,易失粘剥离失效。埋地油气管线剥离防腐层下阴极保护 (CP) 屏蔽和剥离涂层下腐蚀被认为是高绝缘性3PE涂层管线的普遍问题。
水和CO2等腐蚀介质进入涂层剥离区,在管体表面和剥离涂层间形成局部腐蚀环境,成为威胁管道安全运行的重要隐患。3PE涂层透水率差,属非渗透性涂层,3PE涂层与阴极保护系统缺少兼容性,3PE剥离后屏蔽阴极保护电流,剥离防腐层下管体腐蚀可高达0.7 mm/a,NACE建议的评估值为0.4 mm/a。涂层剥离破损可引发管体杂散电流腐蚀、应力腐蚀 (SCC) 和微生物腐蚀 (MIC)等局部腐蚀,其可能引发的风险正受到管线运营企业越来越多的关注。
作者参与的3PE防腐层现场开挖调查表明,涂层剥离一般发生于环氧粉末层/管体界面,始于FBE与管体粘结力降低。目前研究表明:环氧层的粘结失效与环氧粉末材料品质、工厂预制工艺有关。由于使用年限尚短,现场开挖发现防腐层破损点下剥离区周围存在锈痕,由此可判断,由于涂层剥离后尚存抱紧力,地下水渗透剥离区的距离通常仅数厘米,剥离区管体表面尚未出现严重腐蚀迹象。图1示出了部分防腐层现场开挖调查发现的3PE涂层剥离及剥离区管体的腐蚀现象。
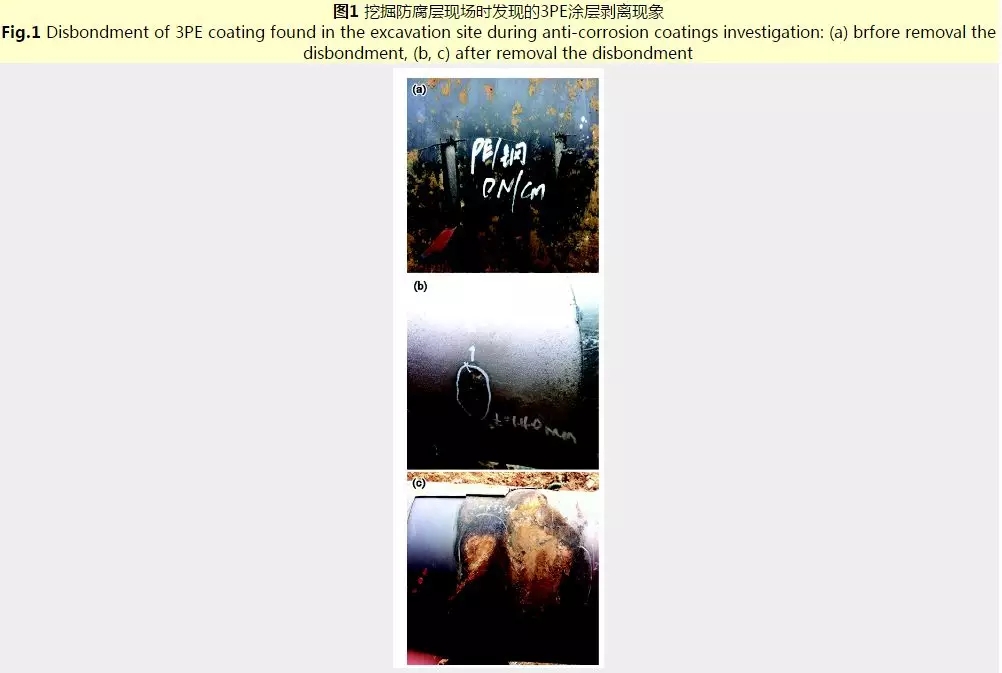
本工作根据管线3PE防腐层失粘剥离的情况及实际工况环境,构建剥离防腐层下管道表面微环境腐蚀模拟实验装置,采用微电极技术监测剥离区管线钢表面的局部电位,研究干湿交替过程工况条件下,剥离防腐层下管道的阴极保护电位/电流分布、阴极保护有效距离及管线钢的腐蚀行为。
1 实验方法
自制的缝隙内SCC实验测试系统由模拟缝隙电解池和加载阵列电极组成,如图2所示。模拟缝隙采用有机玻璃(PMMA)板模拟绝缘性剥离防腐层,模拟剥离区的矩形缝隙池由PMMA盖板、聚四氟乙烯(PTFE)垫片、钢试样及PMMA基板经螺栓组装形成。缝隙厚度可由垫片调节,本研究工作采用1mm。PMMA板一端开方口模拟防腐层破损点(Holiday),缝隙内环境通过该破损点与PMMA板上方储液槽中的本体土壤溶液连通。PMMA板上安装一系列毛细管盐桥及pH微电极,用来测量缝隙内各位置管线钢局部电位。为模拟剥离防腐层下完整管道表面,PMMA基板试样间的空间由5块相同钢制成的辅助板填补。相邻试样间留1 mm间隙并由硅橡胶填充使试样彼此绝缘。实验过程中,所有钢试样和板材通过外部并行线连接。钢试样在底板上的布局如图2所示。盖板、PTFE垫片和试样基板通过螺栓组装,剥离区缝隙周边由硅橡胶密封,以确保缝隙池在实验过程中的密封性。该模拟实验装置的具体方法及过程可见文献。所有实验在室温下完成。
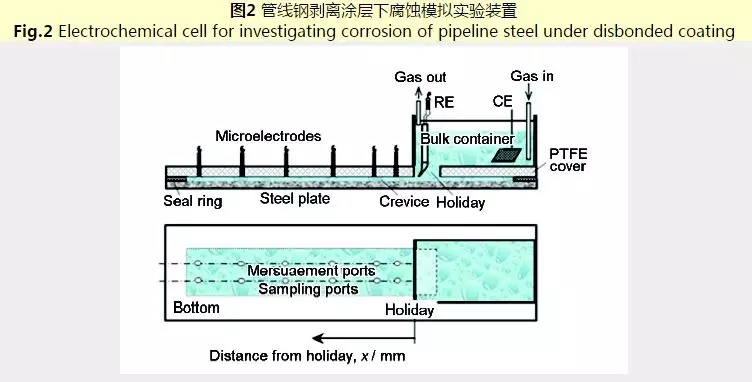
实验材料为X80管线钢,其主要化学成分为 (质量分数,%):C 0.07,Mn 1.82,Si 0.19,P 0.007,S 0.023,Cr 0.026,Ni 0.17,Cu 0.020, Al 0.028, Mo 0.23,Ti 0.012,Nb 0.056,V 0.002,N 0.004,B 0.0001,余量Fe。试样由环氧树脂封固,裸露工作面积为10 mm×10 mm,实验前试样工作表面用水砂纸逐级打磨至1000目,依次用去离子水、丙酮、无水乙醇清洗,吹干,储存于干燥器中备用。
采用沈阳土壤浸出液。土壤取自国家材料环境腐蚀试验站沈阳土壤中心站地下约1 m处。土壤经自然风干后,在105 ℃下干燥10 h,然后机械碾磨后用直径1 mm分析筛进行筛选。土壤溶液采用水土比为1:1的水土混合溶液过滤得到。
模拟土壤干湿交替工况条件,剥离3PE层破损处阴极保护有效保护。首先将剥离涂层X80钢体系全浸在土壤溶液中,一定时间后,将溶液倒出,使体系自然干燥,直至一个干湿循环结束,每个循环为72 h。其中,全浸时间为48 h,干燥时间为24 h,则其干湿交替时间为24 h/48 h,连续进行3个干湿交替循环。
各干湿交替的“湿”过程中,破损点处均施加ECP=-1100 mV阴极保护。阴极保护电位采用HA-301恒电位仪控制,通过鲁金毛细管的饱和甘汞电极(SCE)置于缝口处作为参比电极;使用多通道阴极保护监测系统测量各位置试样的局部电位和电流分布。文中所有电位均为相对于SCE的值。分析剥离涂层下管线钢局部电位变化情况,获得破损处阴极保护有效的保护范围。
实验结束后,剥离区不同位置试样于除锈剂(500mL盐酸+500mL去离子水+20g六次甲基四胺)中去除腐蚀产物,并用去离子水清洗吹干,采用Philips FEGXL30扫描电子显微镜 (SEM) 对剥离区各位置试样表面微观形貌进行观察。
2 结果与讨论
2.1 干湿交替工况环境剥离涂层下阴极保护有效性
干湿交替过程工况条件下,涂层破损点施加-1100 mV阴极保护时,剥离区缝隙内X80钢局部电位和电流分布随时间的变化规律分别示于图3a和b。由图3a可见,涂层破损点处施加-1100 mV阴极保护电位后,缝隙内初试溶液电导率较高,缝内产生了较大的电位梯度,该电位梯度主要集中在破损点附近,剥离区电位处于自然腐蚀电位附近,约-710mV。经历第1个干循环,再次加入溶液并施加阴极保护后,缝隙内45 mm处局部电位逐渐负移至-785 mV,并趋于稳定;缝隙深处局部电位变化不大,仍保持-710mV附近;随极化时间延长,缝隙内电位梯度逐渐减小。随干湿循环次数增加,缝隙内45 mm处稳定后的局部电位逐渐负移,而缝隙深处局部电位变化不大。
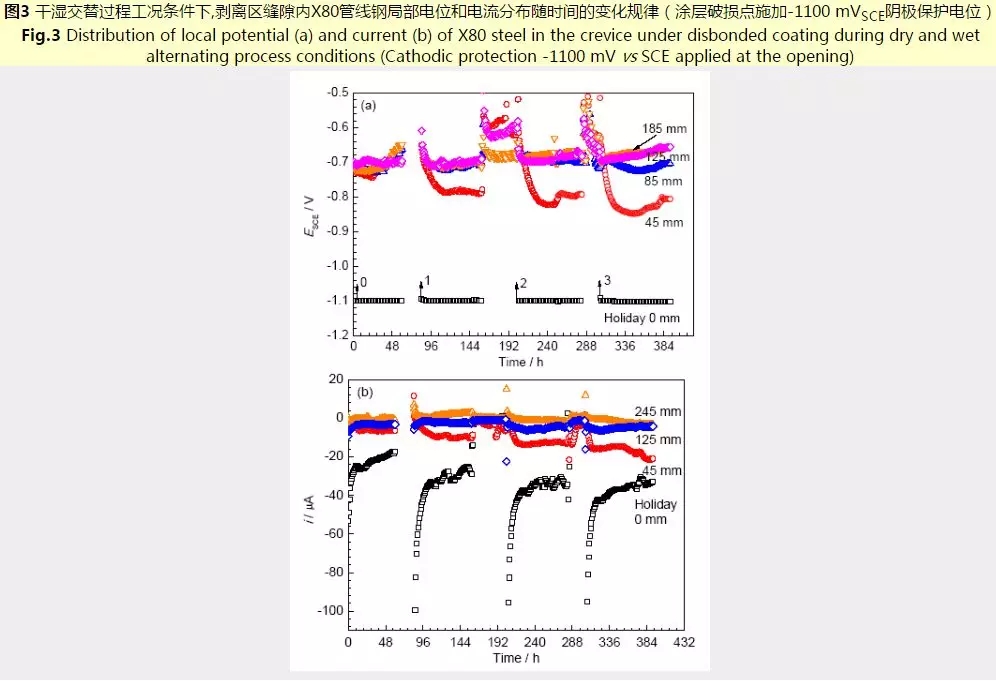
图3b为剥离区X80钢的阴极保护电流随干湿循环次数的变化规律。可见,阴极保护电流主要分布于破损点附近,剥离区位置阴极保护电流非常微小;剥离区内随距离的增加,阴极保护电流逐渐趋于0。随干湿循环次数增加,破损点及缝隙内45 mm处的阴极保护电流有增大趋势。
干湿交替过程中,各干湿周期剥离区X80钢的局部电位和电流分布规律示于图4。可见,阴极保护电位降主要集中在缝隙口附近。经历干湿交替之前,缝内电位由破损点-1100 mV、45 mm处-731 mV随缝隙深度增加逐渐正移至缝底245 mm处-702 mV;若以-850 mVCSE (-780 mVSCE) NACE推荐标准作为最小保护电位的标准,破损点施加ECP=-1100 mV阴极保护电位仅使剥离区内距缝隙口40 mm附近得到了充分阴极保护。经历干湿循环后,缝隙内试样表面腐蚀产物和离子浓度增加,其使缝隙内局部电位和电流分布更均匀,剥离区有效阴极保护距离略有增加,第3周期干湿循环后阴极保护有效范围达50 mm。
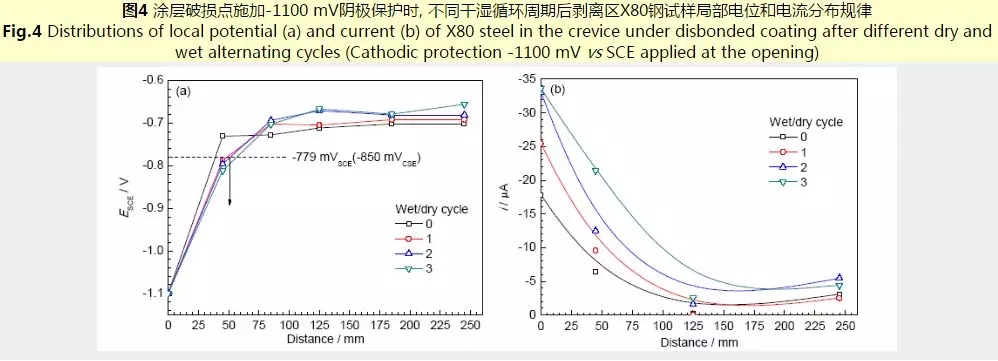
2.2 干湿交替工况环境剥离涂层下X80钢腐蚀形貌
3个干湿交替循环实验结束后,剥离涂层下X80钢各位置试样表面覆有一层疏松腐蚀产物。剥离区不同位置试样腐蚀产物以及除去腐蚀产物后试样表面的SEM腐蚀形貌示于图5。从图中可以看出,剥离区腐蚀产物疏松 (a1~d1);涂层破损点试样主要发生均匀腐蚀 (图5a2,a3),这是由钢的不同冶金显微结构间的电偶效应所致。相比而言,剥离区试样的主要显微特征为局部腐蚀。随剥离区深度增加均匀腐蚀程度逐渐降低,试样出现了点蚀坑,某些区域呈现严重的局部腐蚀形貌 (图5c2,c3,d2和d3)。
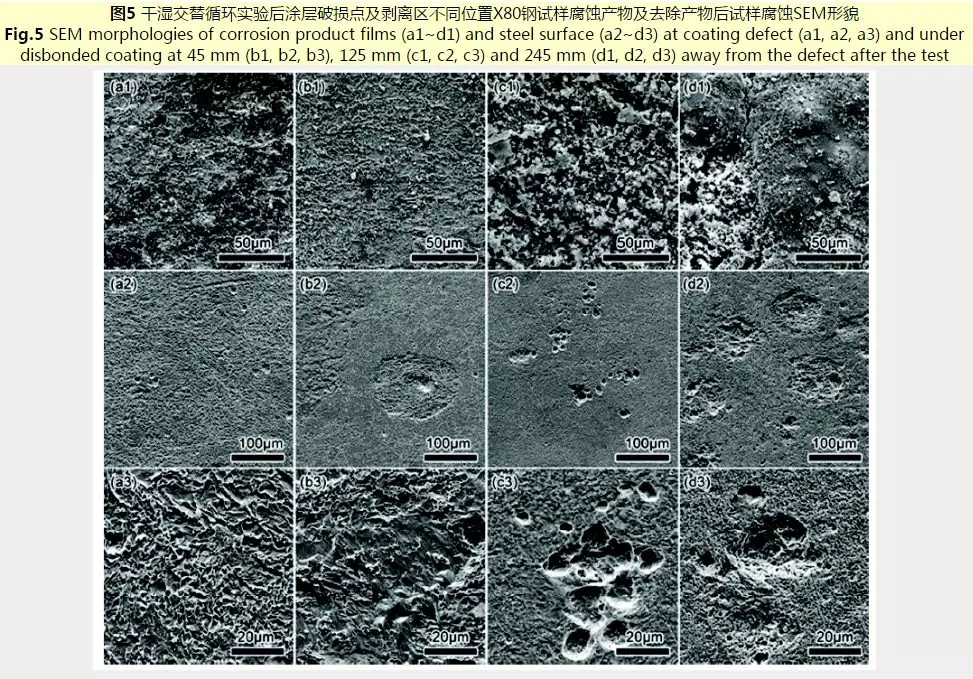
3 结论
(1)带破损点涂层剥离区内阴极保护电位梯度和保护电流主要集中在破损点区域,剥离区深处管线表面处于自然腐蚀状态。
(2)干湿循环过程使缝隙内局部电位和电流分布更加均匀,随干湿循环次数增加,缝隙内45 mm处稳定后的局部电位逐渐负移,缝隙深处局部电位变化不大;破损点及缝隙内45 mm处的阴极保护电流有增大趋势。
(3)经历干循环并施加-1100mV阴极保护电位后,缝隙内钢局部电位逐渐负移并逐渐趋于稳定,电位梯度随极化时间延长逐渐减小。干湿循环过程使缝隙内局部电位和电流分布更加均匀,使剥离区有效阴极保护距离略有增加,阴极保护有效范围达50 mm。
作者:赵君, 闫茂成, 吴长访, 舒韵, 郭爱玲
来源:中国石油管道科技研究中心,中国科学院金属研究所 国家金属腐蚀控制工程技术研究中心,中国石化销售有限公司华中分公司 |